Light weight Canoe
-
- Posts: 23
- Joined: Thu Sep 13, 2007 6:48 pm
- Location: Wiarton Ontario
- Glen Smith
- Posts: 3719
- Joined: Sat May 08, 2004 9:08 am
- Location: Baie-St-Paul, Quebec, Canada
One idea for keeping weight down is to use a light wood like cedar for the gunwales, with only a 1/8" thick strip of harder wood (ash) outside for abrasion resistance. Designed properly, thwarts and seats could also be of cedar, perhaps, in the case of seats, thicker than usual, and with a layer of glass hidden underneath.
You could use 3/16" strips for the bottom and 1/8" strips for the sides, tapering between them, for most of the benefit of each. This would be easier if you used a planed bevel than if you routed bead and flute edges to your strips.
Making sure you have only enough epoxy to fill the cloth, without lots of extra coats, can make a big difference. With the simple curves of a stitch and glue boat, rather than adding extra epoxy and sanding, you can simply cover the cloth wet with epoxy with a plastic film and roll it smooth. This squeezes the glass fibers flat and allows a smooth surface without any second coat at all. In tension, this is just as strong as the standard methods but much lighter. It is a bigger challenge to do this on the compound curves of a woodstrip boat. Using a heavy polyethylene sheeting that had been heated and formed to the canoe before epoxy wetout, I got this to work to some extent, but not as well as I'd like. I don't have a good solution, but I believe the application of the epoxy is an important place to minimize weight with less loss of strength than thinning the strips.
You could use 3/16" strips for the bottom and 1/8" strips for the sides, tapering between them, for most of the benefit of each. This would be easier if you used a planed bevel than if you routed bead and flute edges to your strips.
Making sure you have only enough epoxy to fill the cloth, without lots of extra coats, can make a big difference. With the simple curves of a stitch and glue boat, rather than adding extra epoxy and sanding, you can simply cover the cloth wet with epoxy with a plastic film and roll it smooth. This squeezes the glass fibers flat and allows a smooth surface without any second coat at all. In tension, this is just as strong as the standard methods but much lighter. It is a bigger challenge to do this on the compound curves of a woodstrip boat. Using a heavy polyethylene sheeting that had been heated and formed to the canoe before epoxy wetout, I got this to work to some extent, but not as well as I'd like. I don't have a good solution, but I believe the application of the epoxy is an important place to minimize weight with less loss of strength than thinning the strips.
Alan
- Bryan Hansel
- Posts: 678
- Joined: Fri May 14, 2004 6:36 pm
- Location: Grand Marais, MN
- Contact:
It gets pretty difficult fairing the canoe with 1/8-inch strips, so you'll want to either add stations or just be very careful when you strip the boat. I'd suggest using several layers of 3.2 oz tight weave, instead of one layer of 4 oz. The tight weave soaks up very little epoxy, which ends up with a lighter canoe. If you want a tough canoe, you'll need multiple fabric layers. Here's my layup suggestion:
Inside
1 layer of 3.2 oz. weave glass
1.7 oz. kevlar
1 layer of Innegra S
Core
1/8-inch wood strips
Outside
3 layers of 3.2 oz. weave glass
If you're not going to use your canoe where it could take a beating, then two to three layers of 3.2 oz. weave glass on the inside and outside should be fine.
Inside
1 layer of 3.2 oz. weave glass
1.7 oz. kevlar
1 layer of Innegra S
Core
1/8-inch wood strips
Outside
3 layers of 3.2 oz. weave glass
If you're not going to use your canoe where it could take a beating, then two to three layers of 3.2 oz. weave glass on the inside and outside should be fine.
- Redbird Bernie
- Posts: 28
- Joined: Sun Oct 17, 2010 3:14 pm
- Location: Illinois, USA
Everybody, thanks for all the wonderful suggestions.
Bryan, exactly what do you mean by "it gets pretty difficult fairing the canoe with 1/8 inch strips"? Are you specifically referring to the fact that the hull will be unusually soft with a lot of give which will make sanding difficult?
I don't yet know if it is wise to use 1/8 inch strips. For sure I'll need to review the many alternatives, do a little math and some testing. Come to think of it, there must be test data available somewhere for various combinations of cloth, core and epoxy thickness.
Bryan, exactly what do you mean by "it gets pretty difficult fairing the canoe with 1/8 inch strips"? Are you specifically referring to the fact that the hull will be unusually soft with a lot of give which will make sanding difficult?
I don't yet know if it is wise to use 1/8 inch strips. For sure I'll need to review the many alternatives, do a little math and some testing. Come to think of it, there must be test data available somewhere for various combinations of cloth, core and epoxy thickness.
epoxy strength strip thickness chart
Here is the chart - I got this 3 years ago from 'Rapt' over on the myccr forum.
Moonman
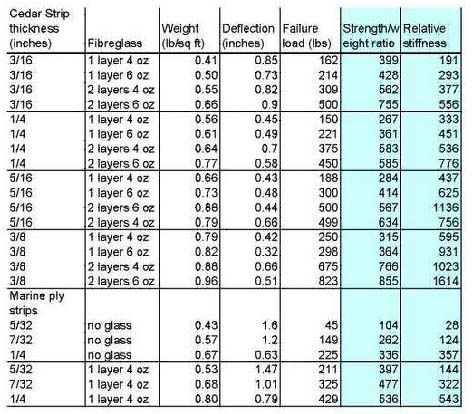
Moonman
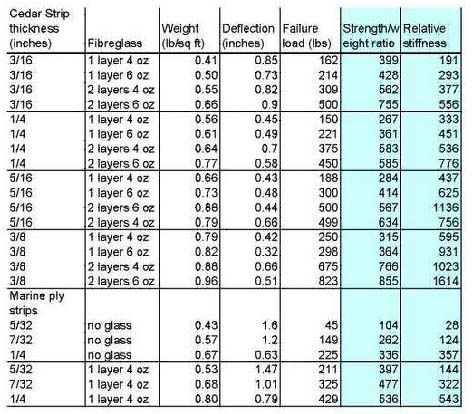
- Bryan Hansel
- Posts: 678
- Joined: Fri May 14, 2004 6:36 pm
- Location: Grand Marais, MN
- Contact:
There's not much wood in a 1/8" strip, so you won't be able to sand the surface as much as you would with thicker strips, and the hull gives more than it would with thicker strips while sanding. What I found when building with 1/8" strips was just to take extra time to make sure the strips were as close to fair as possible while striping the hull. I'd suggest spacing station at 10" intervals instead of 12". That'll help while sanding and it'll help get a fair shape while stripping.Redbird Bernie wrote:Bryan, exactly what do you mean by "it gets pretty difficult fairing the canoe with 1/8 inch strips"? Are you specifically referring to the fact that the hull will be unusually soft with a lot of give which will make sanding difficult?
Here's a few more ideas:
Another way to save weight is during the selection of your wood--different boards from the same species vary in weight. Go for the lightest.
Wood varies in stiffness. Check your strips to see how easy they bend. Strips that bend less are stiffer, so use those in areas, like the floor that need extra stiffness.
All epoxies are not created equal. You want to find one that is stiff, hard and abrasion resistant.
You'll save lots of weight in trim.
You aluminum brackets and pop rivets to make a platform for the seats.
Consider aluminum gunwales, thwarts, seats. Black looks nice when contrasted with the wood.
- Redbird Bernie
- Posts: 28
- Joined: Sun Oct 17, 2010 3:14 pm
- Location: Illinois, USA
Thanks Moonman, that’s great information. Stuff like this is obviously available to designers but I’ll be darn if I could find it. Granted, I have not contacted any cloth or epoxy manufacturers.
Bryan, all good suggestions.
Relative to spacing the stations 10" apart, I'd pretty much need the forms at 12" to start with in order to create the new forms for 10". Given the circumstances it might be just as well to make them for 6".
You bring out an interesting point. The differences in density from one piece of WRC to the next are not generally a problem but might become one when using 1/8 inch strips and grouping the less stiff and dense stuff all above the waterline. What is unknown are the properties of the less dense WRC in comparison to the stiffer and denser WRC. I’m thinking that denser 1/4 inch thick WRC might possibly end up being equivalent in strength, stiffness, shear strength, etc. to 3/16 inch WRC. Woods of all kinds have been tested extensively through the years so that’s something to research and find.
I hadn’t given any thought to aluminum as a building material to tell the truth . It may make sense to sister or sandwich aluminum pieces to wood in order to augment strength and keep weight down. Naturally thermal expansion would need to be considered. I wonder if aluminum would stain the wood in time.
Bryan, all good suggestions.
Relative to spacing the stations 10" apart, I'd pretty much need the forms at 12" to start with in order to create the new forms for 10". Given the circumstances it might be just as well to make them for 6".
You bring out an interesting point. The differences in density from one piece of WRC to the next are not generally a problem but might become one when using 1/8 inch strips and grouping the less stiff and dense stuff all above the waterline. What is unknown are the properties of the less dense WRC in comparison to the stiffer and denser WRC. I’m thinking that denser 1/4 inch thick WRC might possibly end up being equivalent in strength, stiffness, shear strength, etc. to 3/16 inch WRC. Woods of all kinds have been tested extensively through the years so that’s something to research and find.
I hadn’t given any thought to aluminum as a building material to tell the truth . It may make sense to sister or sandwich aluminum pieces to wood in order to augment strength and keep weight down. Naturally thermal expansion would need to be considered. I wonder if aluminum would stain the wood in time.
Bernie,
I wouldn't be too worried about density of one board over another if concerned about strength. I would actually go lighter boards wherever I could, especially if you are talking about 3/16" strips. Remember that composite boats are often made with their laminate fabrics only (Kevlar etc.) with no real 'thickness". Sometimes foam is added in strategic areas to stiffen the hull - increased beam profile. Yes sometimes some composite boats can oil can a bit, but for the most part they still hold up just fine. When you compare a strip built boat to a composite boat you can see the stripper is almost always A LOT stiffer. Another aspect is that strip built boats almost always have epoxy as the resin. Composites are almost always using (cheaper) vinylester resins which are not as strong as epoxy.
So while you do have trade-offs with strength issues when trimming down strip thickness, and have to be careful about dynamic impacts, especially on the inside, the overall boat should be still plenty strong.
Moonman
I wouldn't be too worried about density of one board over another if concerned about strength. I would actually go lighter boards wherever I could, especially if you are talking about 3/16" strips. Remember that composite boats are often made with their laminate fabrics only (Kevlar etc.) with no real 'thickness". Sometimes foam is added in strategic areas to stiffen the hull - increased beam profile. Yes sometimes some composite boats can oil can a bit, but for the most part they still hold up just fine. When you compare a strip built boat to a composite boat you can see the stripper is almost always A LOT stiffer. Another aspect is that strip built boats almost always have epoxy as the resin. Composites are almost always using (cheaper) vinylester resins which are not as strong as epoxy.
So while you do have trade-offs with strength issues when trimming down strip thickness, and have to be careful about dynamic impacts, especially on the inside, the overall boat should be still plenty strong.
Moonman
- Patricks Dad
- Posts: 1476
- Joined: Wed Oct 13, 2004 1:11 pm
- Location: Warrenville, Illinois
Moonman,
The table you posted is very interesting. I'm sneaking up on a glassing job and am considering 4 oz glass to save weight. But looking at the table I see 150 lb in the "failure Load" column (1/4" strips). I'm not sure what that actually means but as a guy who weighs over 180, it makes me wonder if 4 oz glass is a good idea. For a <10% increase in weight (.61 vs .56 lbs/sq ft) there is a significant increase in failure load (150 --> 221 lbs).
I would appreciate any advice on interpreting the table.
thanks!
The table you posted is very interesting. I'm sneaking up on a glassing job and am considering 4 oz glass to save weight. But looking at the table I see 150 lb in the "failure Load" column (1/4" strips). I'm not sure what that actually means but as a guy who weighs over 180, it makes me wonder if 4 oz glass is a good idea. For a <10% increase in weight (.61 vs .56 lbs/sq ft) there is a significant increase in failure load (150 --> 221 lbs).
I would appreciate any advice on interpreting the table.
thanks!
Hi Randy,
On the myccr forum where I got the chart from the poster Rapt, he did give an explanation of the chart, as well I think he added some info from the original chart in the West Systems Epoxyworks magazine. I will see if I can find the old thread and maybe post that info here - stay tuned!
Moonman
On the myccr forum where I got the chart from the poster Rapt, he did give an explanation of the chart, as well I think he added some info from the original chart in the West Systems Epoxyworks magazine. I will see if I can find the old thread and maybe post that info here - stay tuned!
Moonman
Hi Randy,
Found the thread - easier than I thought it would be. Here is what rapt had to say when he posted the chart (I hope he doesn't mind me posting his words here):
"I tracked down the data from Epoxyworks with the strengths for various cedar glass epoxy layups. They were done with West epoxy, in 12" squares and then cured fo 60 days, and weighed carefully before being tested on an MTS machine.
The deflection data is how far the sample was flexed at the point of failure.
The table I have attached is the same data as in Epoxyworks #10, pg 5. But I've also added a couple calculated columns (shaded) and sorted the data slightly differently.
The things I think are of key importance are the 3/16" strip and single 6 oz glass layup and dual 4 oz glass layup as compared to the 1/4" strip and single layer of 6 oz... The strengths of the two 6 oz combinations is so close as to be negligible in difference. However the 3/16" strips give a significantly lighter weight for the same strength. Using two layers of 4 oz with 3/16" strips gives greater strength and still weighs slightly less than the "standard" 1/4" and 6oz.
Food for thought for builders.
If you plan on using your hull lightly then 3/16" and 4 oz is as strong as and significantly lighter than 1/4" and 4 oz.
Further 3/16" inch thickness seems to be the sweet spot in terms of strip thickness for strength and weight. Even for higher strengths requirements. Its only when the requirements become "extreme" in strength or stiffness, that thicker strips gain anything and that requires going to 3/8" strips to exceed the capability of the 3/16" strips."
Also, the link to the actual thread is here:
http://www.myccr.com/SectionForums/view ... lit=+epoxy
hope that helps.
Moonman.
Found the thread - easier than I thought it would be. Here is what rapt had to say when he posted the chart (I hope he doesn't mind me posting his words here):
"I tracked down the data from Epoxyworks with the strengths for various cedar glass epoxy layups. They were done with West epoxy, in 12" squares and then cured fo 60 days, and weighed carefully before being tested on an MTS machine.
The deflection data is how far the sample was flexed at the point of failure.
The table I have attached is the same data as in Epoxyworks #10, pg 5. But I've also added a couple calculated columns (shaded) and sorted the data slightly differently.
The things I think are of key importance are the 3/16" strip and single 6 oz glass layup and dual 4 oz glass layup as compared to the 1/4" strip and single layer of 6 oz... The strengths of the two 6 oz combinations is so close as to be negligible in difference. However the 3/16" strips give a significantly lighter weight for the same strength. Using two layers of 4 oz with 3/16" strips gives greater strength and still weighs slightly less than the "standard" 1/4" and 6oz.
Food for thought for builders.
If you plan on using your hull lightly then 3/16" and 4 oz is as strong as and significantly lighter than 1/4" and 4 oz.
Further 3/16" inch thickness seems to be the sweet spot in terms of strip thickness for strength and weight. Even for higher strengths requirements. Its only when the requirements become "extreme" in strength or stiffness, that thicker strips gain anything and that requires going to 3/8" strips to exceed the capability of the 3/16" strips."
Also, the link to the actual thread is here:
http://www.myccr.com/SectionForums/view ... lit=+epoxy
hope that helps.
Moonman.
- Redbird Bernie
- Posts: 28
- Joined: Sun Oct 17, 2010 3:14 pm
- Location: Illinois, USA
Hey Moonman,
According to Ted Moores (Canoecraft page 69):
“We found that ¼ inch cedar between layers of 6 oz glass cloth did not fail until subjected to a load of 221 lbs. An additional layer of 6 oz cloth (such as might be applied to a canoe’s bottom) increased the failure point by more than 100% (to 459 lbs), though it added only 25% more weight.”
Obviously his findings of 221 lbs failure load for ¼ “ cedar with 2 layers of cloth are short of the 375 lbs figure found in the Epoxyworks #10 chart.
I found a comment by Garland Reese (see http://www.kayakforum.com/cgi-bin/Build ... view=18778 ) stating “that the (Epoxyworks) data is too scattered to be of any use. That is, the data does not agree well with engineering models, such as PB&J”. To which Nick Shade (see http://www.kayakforum.com/cgi-bin/websearch.pl ) replied: “Apparently, this data came from an article by J.R. Watson, and was > published in "Epoxyworks", Number 10 (winter '98). This is the same data I refer to in my book. While it seems to be the only/best data around, it is rather limited. I was forced to be rather "mealy mouthed" when refering to the data. I expect Ted was felt constrained in what conclusions he could draw from the data. There is not enough data to say X layup is "best" for Y purpose”.
I could not find the original Epoxyworks #10 text but in any case, based on the opinions of experienced builders the chart is not to be trusted.
Bernie
According to Ted Moores (Canoecraft page 69):
“We found that ¼ inch cedar between layers of 6 oz glass cloth did not fail until subjected to a load of 221 lbs. An additional layer of 6 oz cloth (such as might be applied to a canoe’s bottom) increased the failure point by more than 100% (to 459 lbs), though it added only 25% more weight.”
Obviously his findings of 221 lbs failure load for ¼ “ cedar with 2 layers of cloth are short of the 375 lbs figure found in the Epoxyworks #10 chart.
I found a comment by Garland Reese (see http://www.kayakforum.com/cgi-bin/Build ... view=18778 ) stating “that the (Epoxyworks) data is too scattered to be of any use. That is, the data does not agree well with engineering models, such as PB&J”. To which Nick Shade (see http://www.kayakforum.com/cgi-bin/websearch.pl ) replied: “Apparently, this data came from an article by J.R. Watson, and was > published in "Epoxyworks", Number 10 (winter '98). This is the same data I refer to in my book. While it seems to be the only/best data around, it is rather limited. I was forced to be rather "mealy mouthed" when refering to the data. I expect Ted was felt constrained in what conclusions he could draw from the data. There is not enough data to say X layup is "best" for Y purpose”.
I could not find the original Epoxyworks #10 text but in any case, based on the opinions of experienced builders the chart is not to be trusted.
Bernie
- Bryan Hansel
- Posts: 678
- Joined: Fri May 14, 2004 6:36 pm
- Location: Grand Marais, MN
- Contact:
If you modeled the boat in Delftship, you could output stations at 10" without having to build 12" forms. Every 6" would probably be easier and that spacing should prevent any sanding deflection.
I don't see any staining on my kelvar boats from the aluminum.
I think the Epoxyworks chart is interesting, but, in my experience, the type of damage to worry about is usually abrasion vs. impact. The way I've addressed that is via a harder epoxy and more layers of fabric.
You mention using a 4 oz. glass for a project, you're working on. I'd gamble that if you switched to two layers of 3.2 oz. tight weave, you'd end up with a stronger boat at the same weight. I've always found I use less epoxy with a tight weave.
I don't see any staining on my kelvar boats from the aluminum.
I think the Epoxyworks chart is interesting, but, in my experience, the type of damage to worry about is usually abrasion vs. impact. The way I've addressed that is via a harder epoxy and more layers of fabric.
You mention using a 4 oz. glass for a project, you're working on. I'd gamble that if you switched to two layers of 3.2 oz. tight weave, you'd end up with a stronger boat at the same weight. I've always found I use less epoxy with a tight weave.